1. Introduction to Ozone Treatment
Overview of Ozone and Its Importance in Water Treatment
Ozone (O₃) is a molecule composed of three oxygen atoms and is recognized as one of the most powerful oxidants used in water treatment. Its ability to participate in redox reactions allows it to effectively treat water through both disinfection and oxidation processes. Ozone is particularly valued in water treatment due to its efficiency in inactivating pathogens and its potential for improving water quality by oxidizing organic and inorganic contaminants.
Ozone cannot be stored because of its instability; it must be generated on-site at treatment facilities. Once produced, it is immediately injected into the water, where it dissolves and begins reacting with the constituents present. Ozone’s primary function in water treatment is to enhance the safety and quality of potable water, while also supporting regulatory compliance.
How Ozone is Generated and Used in Water Treatment
Ozone is produced when oxygen (O₂) molecules are split by an energy source, such as ultraviolet (UV) light or an electrical discharge, and recombine with oxygen atoms to form ozone (O₃). The typical method of ozone generation in water treatment plants is via the corona discharge process, where oxygen gas is passed through an electrical field, causing the oxygen molecules to split and reform as ozone.
Once generated, ozone is injected into water, dissolving almost immediately. Ozone reacts with a wide range of compounds, including organic material, to disinfect and oxidize harmful contaminants. It decays back into oxygen relatively quickly after completing its reactions, leaving no residuals in the water. This lack of residual disinfection capability requires the use of additional disinfectants, such as chlorine, for continued protection in the distribution system.
Advanced Oxidation Processes (AOP) Expansion
In addition to its powerful role in disinfection and oxidation, Advanced Oxidation Processes (AOPs) further enhance water treatment by generating hydroxyl radicals (OH·), which have a higher oxidation potential than ozone alone. These radicals are capable of breaking down stubborn contaminants, such as trace organic compounds (TOCs), pharmaceuticals, and pesticides, which are resistant to traditional treatment methods.
One of the most widely applied AOPs in water treatment is the peroxone process (O₃/H₂O₂), where ozone is combined with hydrogen peroxide to accelerate the formation of hydroxyl radicals. This process is especially useful for treating water that contains complex organic pollutants, as the hydroxyl radicals rapidly degrade these compounds into smaller, less harmful molecules. This makes AOPs highly effective in advanced water reuse applications where strict water quality standards must be met.
AOPs also enhance the performance of downstream filtration systems, such as biological activated carbon (BAC). By breaking down organic matter before it enters these filters, AOPs reduce the organic load, improving filtration efficiency and prolonging filter lifespan. The synergy between AOP and filtration ensures a higher quality of treated water, making this approach both effective and economical for improving water quality, particularly in challenging wastewater or potable reuse scenarios.
Module Goals: Theory, Operation, and Compliance
This module is designed to provide a comprehensive understanding of ozone treatment systems, focusing on the theoretical principles, operational practices, and regulatory compliance required for ozone application in water treatment. The key learning objectives include:
- Understanding the chemistry and behavior of ozone in water.
- Recognizing the different system configurations used to generate and apply ozone.
- Learning the operational techniques required to maintain ozone treatment systems effectively.
- Preparing for certification exams by mastering ozone-related calculations and safety protocols.
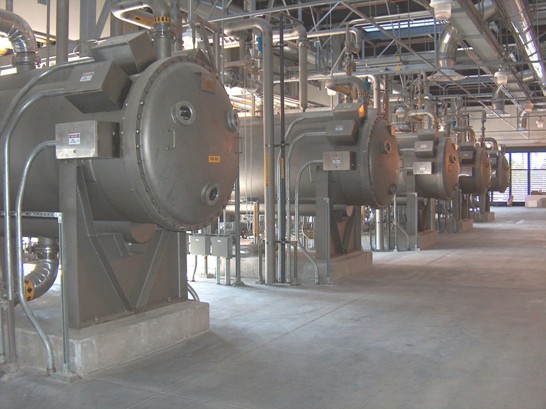